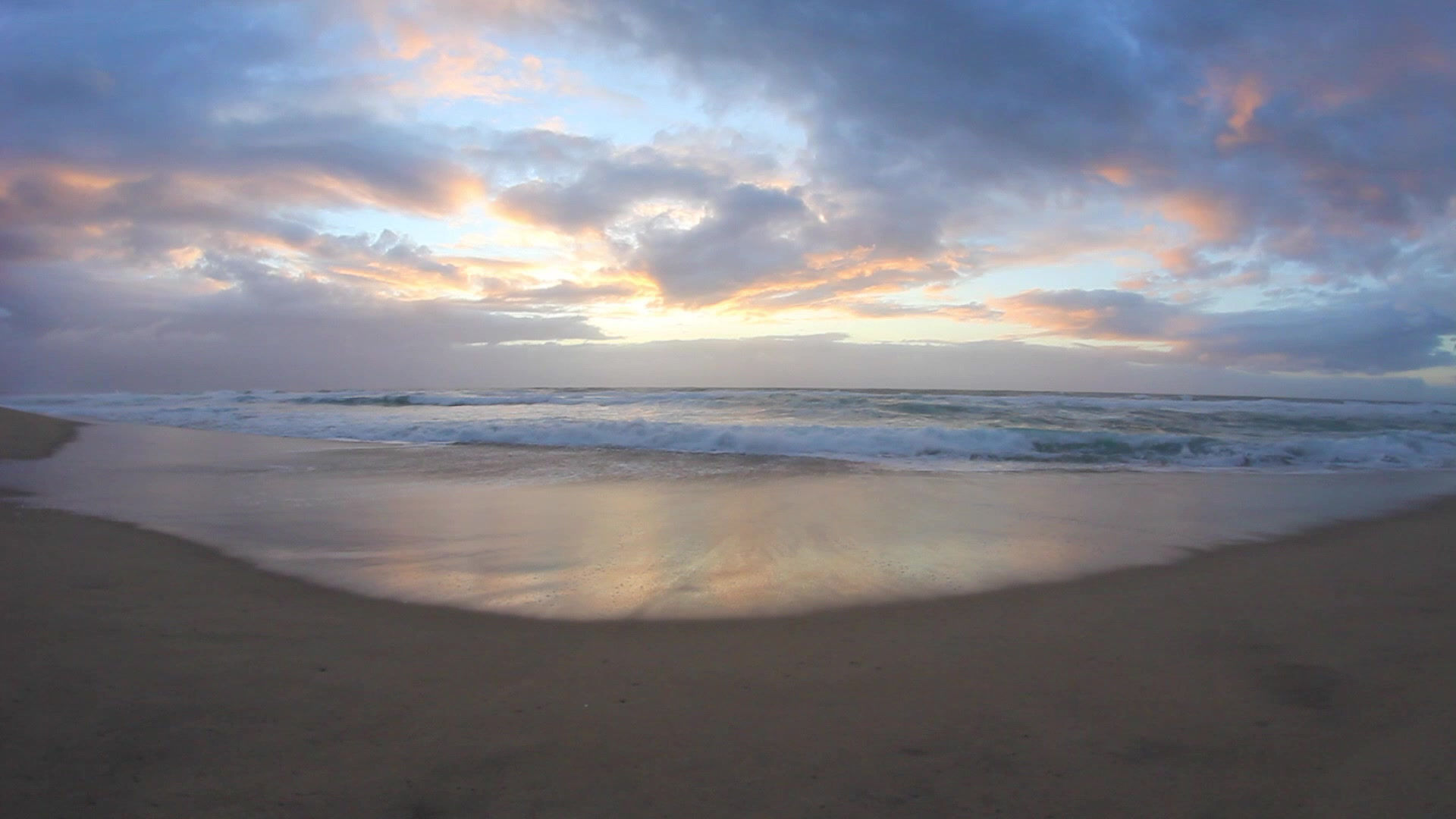
UASTRO & com.
KEYNOTE SPEAKERS 2025

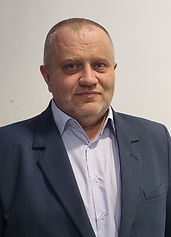

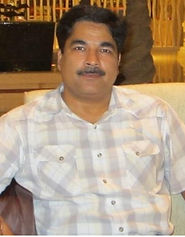
Prof.univ.Liang Guozhu Prof.univ. Luige Vladareanu Dr.eng. Emanuel Pop Prof.univ. Usman Qayum Prof.univ. Muhammad Ushaq
BUAA UNIV. CHINA IMS-Romanian Academy AFT Company -ROMANIA CESAT Company-PAKISTAN CESAT Company- PAKISTAN




​Prof.univ.Afshin Banazadeh Prof.univ.Vlad Muresan Ph.D.Eng. Liu Yiping Dr.Ramona Constantinescu Prof.univ. Sajid Baloch
Sherif Univ. IRAN Teh.univ. Cluj-Napoca ROMANIA BUAA univ. China Pol.Vitan ROMANIA CESAT-PAKISTAN
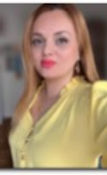




Prof.univ. Gabi Jiga Prof.univ. Adrian Olaru Ph.D. Sun Yeshen
UNSTPB- Romania UNSTPB- Romania BUAA univ.China
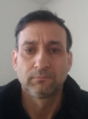
Prof.univ. Vasile Dobref Prof.univ. Florin Mingireanu Prof.univ. Bisu Claudiu
Naval Academy- Romania ROSA- Romania NUSTPB- Romania

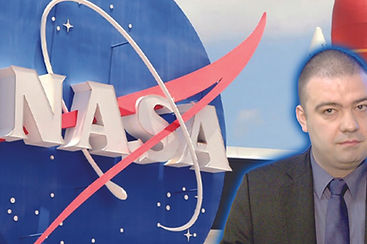